Generally a designer will specify a range of joins that will suit the boat which include scarf and buttstrap joints. What are the advantages and disadvantages?
Butt joins with Buttstraps for plywood boats. Also called Butt blocks.
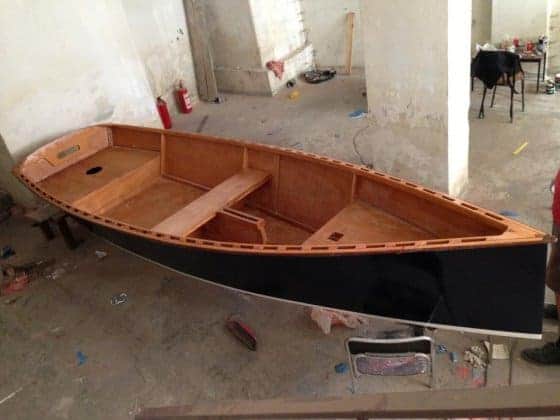
I specify butt straps because they are simpler, faster and have a neat result for amateurs every time. But I do place them in the hull where they won’t affect curvature of the ply. Goat Island Skiff above shows butt straps joining the ply near the middle of the boat. It was built in Greece by Snare Drum Spies.
Scarf joins in plywood boats

Boats where the plywood has high curvature in the join area have no choice. Butt straps will change the stiffness of the plywood. So scarfs are the way to go.

Scarfs are the only join that doesn’t affect the ability of the ply to form a rounded shape hull.
Also clinker or lapstrake boats have so many planks to join it can look ugly if butt straps are used on every plank.
Advantages of Butt straps for ply boatbuilding
- Perfect alignment every time for both the angle of the join and getting the surfaces flush. Scarf joins have a whole range of positions for the two pieces of ply. Butts have no choice.
- Butt straps require almost no skillset to make work.
- The outside glue join of butts is hair width. Scarfs are at a 6:1 or more angle so the glue join will be six times wider
- Butt straps are very fast. Cut the block, put the ply to be joined down flat, mark the position of the butt and glue away.
- Butt straps are one step and require no filling. Every other type of home buildable join is multiple stages of work.
- The biggest “downside” of buttstraps is that they are visible sometimes. But the reality is people seldom see them or classify them as something “wrong” with the boat.
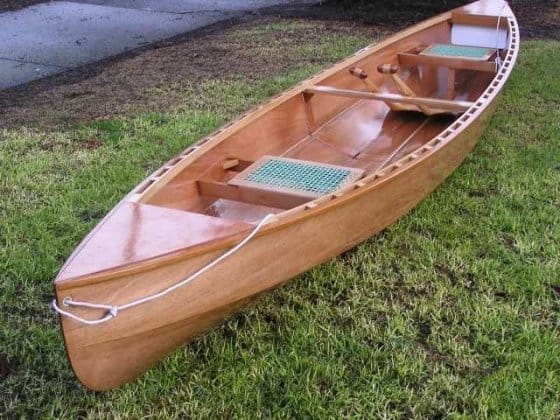
As far as scarfs go … I choose butt straps every time possible because they result in a perfect clean join on the outside of the boat and make sure that the panels align properly because it is a hard edge against hard edge.
Perfect for first time amateur boatbuilding.
Scarfs are not very easy to get right in plywood. The glue line is much larger as the join has a shallow angle to the and often there are slight differences in levels at different parts of the scarf join which need filling later. With a butt strap those problems are gone.
There is a choice in designing a boat. Use some of the length of the boat for scarfs, or build a longer boat for the same amount of plywood. The second always looks like the best choice.
However, many of the premium European Gaboon plywoods are a slightly longer sheet. Standard sheets are 2440 in metric, but most gaboon or mahogany ply from Europe is 2500. Giving you an extra 60mm or 2 3/8″ for a scarf. Normal ply scarfs are 1:6, so for 6mm ply you need 36mm or 1 1/2″. Or less if thinner ply.
My summary would be that if you just want to build a boat then go with the butts. If you want to extend your boatbuilding skill range then give scarfs a try.
Useful knowledge for making robust scarf joins
When gluing a scarf join in ply or timber you are always gluing Endgrain. Precoating immediately before assembly is essential.

The basic problem is that end grain is highly absorbent so it can steal the resin from the join leaving insufficient for good bonding. The trick … is to feed the end grain some mixed resin before the glue mix is put on
Remember that generally epoxy needs to have the correct powder modifier added to the mixed resin and hardener for most types of gluing.
When gluing endgrain with epoxy it is a two stage process.
1/ Mix enough resin and hardener to do the job. Stir well. Brush the mixed epoxy onto the endgrain.
2/ Wait 5 minutes. This allows the epoxy to soak in. Brush more epoxy on the endgrain.
3/ Now add the high strength gluing powder to the epoxy in the container and apply to gluing surfaces.
4/ And hold in place by normal method – clamps or temporary fasteners or tape until the epoxy sets up.
There are other joins, what about them?
I’ve used just about every sort of join in either building or repair work. But buttstraps are faster and require no messing around for straight ahead boat building.
I do find glass tape joins are very useful for hole repairs where they can make repairs easier and have a very neat result without any complicated shaping. But for boatbuilding they have too many stages over too much of the boat.
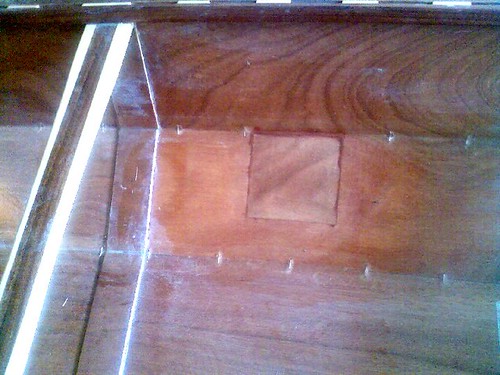
One type of join I think is usually retrograde are jigsaw or puzzle joins.
They have enough strength for handling while building the boat but often require glass on one or both sides for full strength. Again adding to labour and general mess. I am not a fan of adding much glass to boats and the trend to glassing recreational ply kayaks inside and out is very retrograde, adding weight, labour and complexity to what should be a very simple and light boat. It was never required until recently. Expedition boats, yes, for surf landings onto rock shelves.
Some say glassing “doesn’t add much weight” but I have to lug glassed and unglassed boats of the same type around the workshop or for portages and I would minimise or eliminate glass at every point. It is an oft repeated myth.